Bearings are annular parts of a thrust rolling bearing with one or several raceways. Fixed end bearings use radial bearings capable of carrying combined (radial and axial) loads. These bearings include: deep groove ball bearings, double row or paired single row angular contact ball bearings, self-aligning ball bearings, spherical roller bearings, matched tapered roller bearings, NUP type cylindrical roller bearings or with HJ angle rings NJ type cylindrical roller bearings.
In addition, the bearing arrangement at the fixed end can contain a combination of two bearings:
1. Radial bearings that can only bear radial loads, such as cylindrical roller bearings with one ring without ribs.
2. Bearings that provide axial positioning, such as deep groove ball bearings, four-point contact ball bearings or bidirectional thrust bearings.
Bearings used for axial positioning must not be used for radial positioning, and usually have a small radial clearance when installed on the bearing seat.
Bearing manufacturers remind: There are two ways to accommodate the thermal displacement of the floating bearing shaft. The first thing to do is to use a bearing that only accepts radial loads and allows axial displacement to occur inside the bearing. These bearings include: CARB toroidal roller bearings, needle roller bearings and a cylindrical roller bearing without ribs. Another method is to use a radial bearing with a small radial clearance when mounted on the housing so that the outer ring can move freely axially.
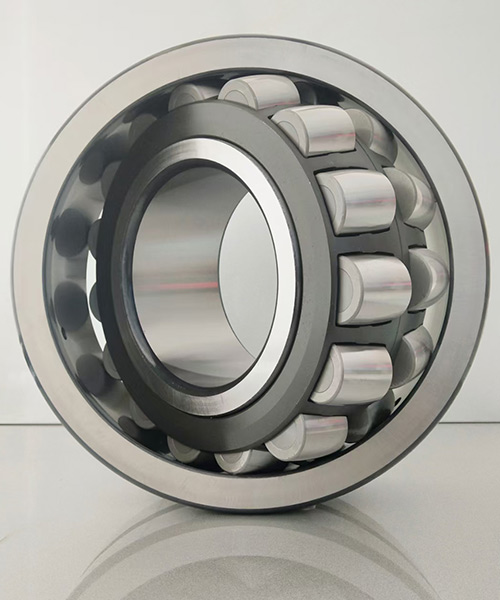
1. Lock nut positioning method:
When the inner ring of a bearing with an interference fit is installed, one side of the inner ring is usually placed against the shoulder on the shaft, and the other side is generally fixed with a lock nut (KMT or KMTA series). Bearings with tapered bores are mounted directly on tapered journals, usually secured to the shaft with a locknut.
2. Spacer positioning method:
It is convenient to use spacers or spacers between bearing rings or between bearing rings and adjacent parts, instead of integral shaft or housing shoulders. In these cases, dimensional and form tolerances also apply to the associated part.
3. Positioning of stepped bushing:
Another method of bearing axial positioning is to use stepped bushings. Ideal for precision bearing arrangements, these bushings offer less runout and higher accuracy than threaded locknuts. Stepped bushings are often used in very high-speed spindles for which conventional locking devices cannot provide sufficient accuracy.
4. Fixed end cap positioning method:
When the Wafangdian bearing is installed with an interference fit bearing outer ring, usually one side of the outer ring is against the shoulder on the bearing seat, and the other side is fixed with a fixed end cover. The fixed end cover and its set screw negatively affect bearing shape and performance in some cases. If the wall thickness between the housing and the screw holes is too small, or if the screws are tightened too tightly, the outer ring raceway may be deformed. The lightest ISO size series, series 19, is more susceptible to this type of damage than series 10 or heavier.
Post time: Jul-25-2022