Factory
With our state-of-the-art production equipment, we have the capability to produce a range of bearings in sizes from 80mm to 2000mm in diameter. Our advanced manufacturing process ensures that every aspect of production, from raw material to finished product, is meticulously controlled and monitored.
Our all-inclusive production capabilities allow us to offer bearings at a lower cost without sacrificing quality. Each step of the manufacturing process is carried out with the utmost precision and efficiency, resulting in a superior product that meets our customers' needs.
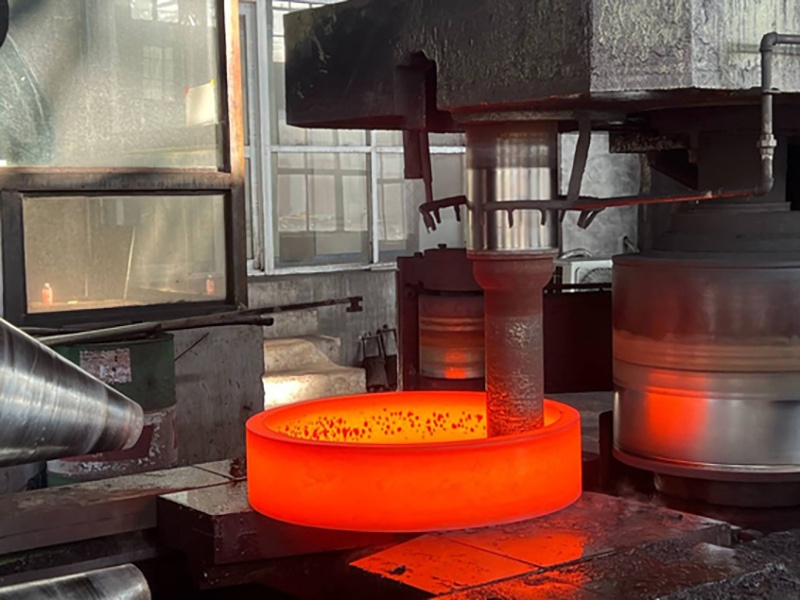

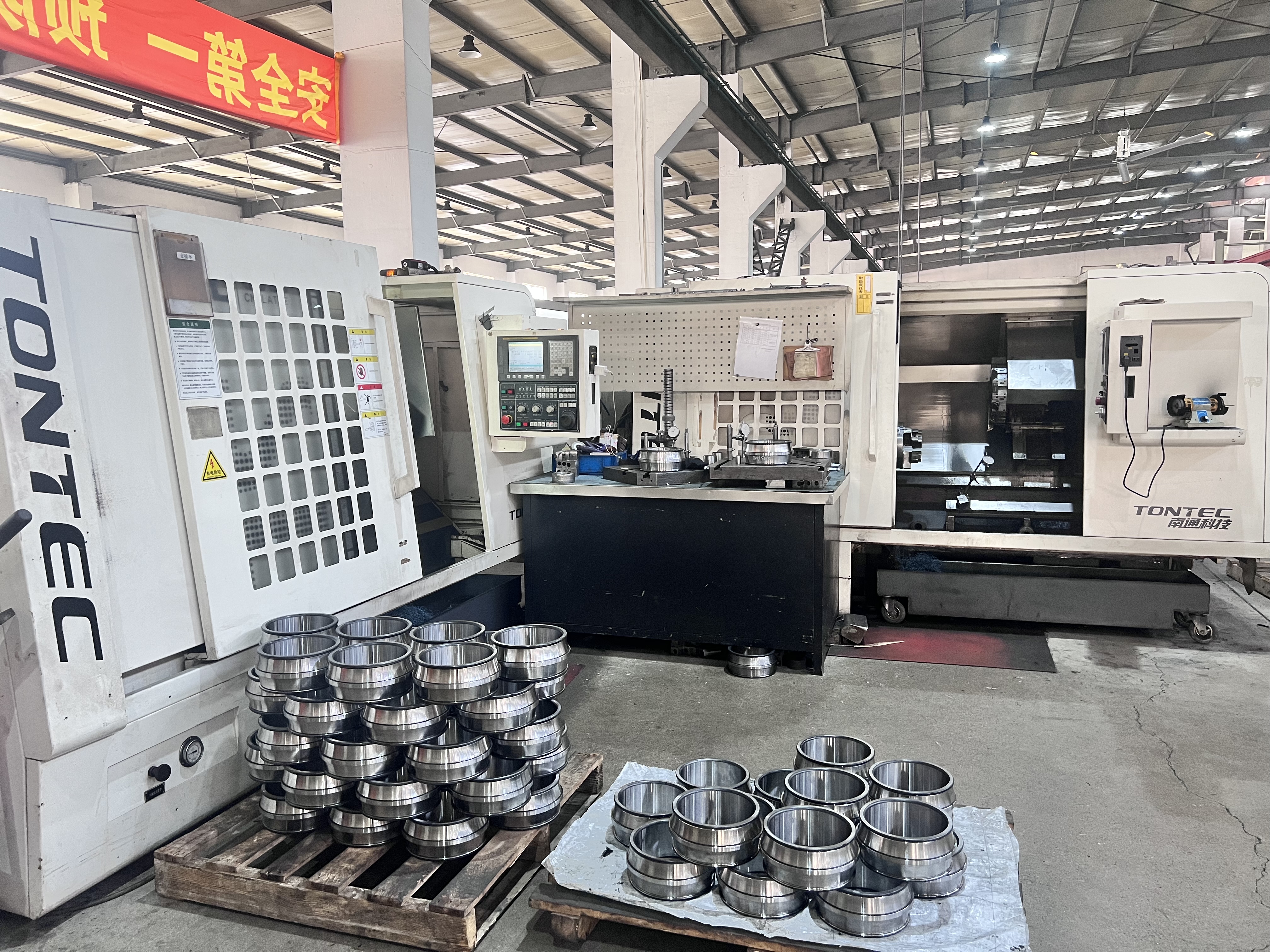
Forging machine
800 ton press and 400 ton press, vertical grinding ring and ensuring the density and quality of forgings.
Spheroidizing annealing of forgings
The performance of the equipment is stable, and a uniform spheroidized structure can be obtained, which is not ready for subsequent turning and quenching
CNC inclined lathe
Dual station, high-precision, inclined bed, one feeding, efficient, with a deviation of less than 0.03mm.
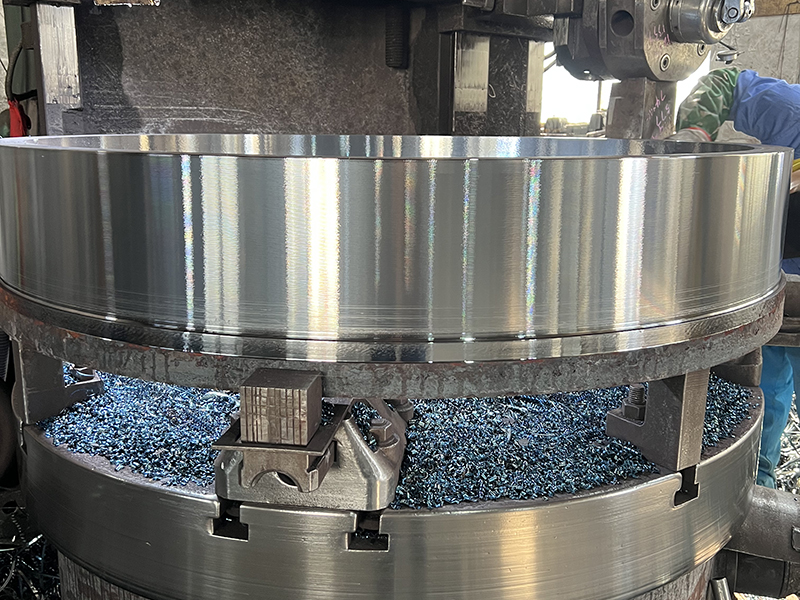
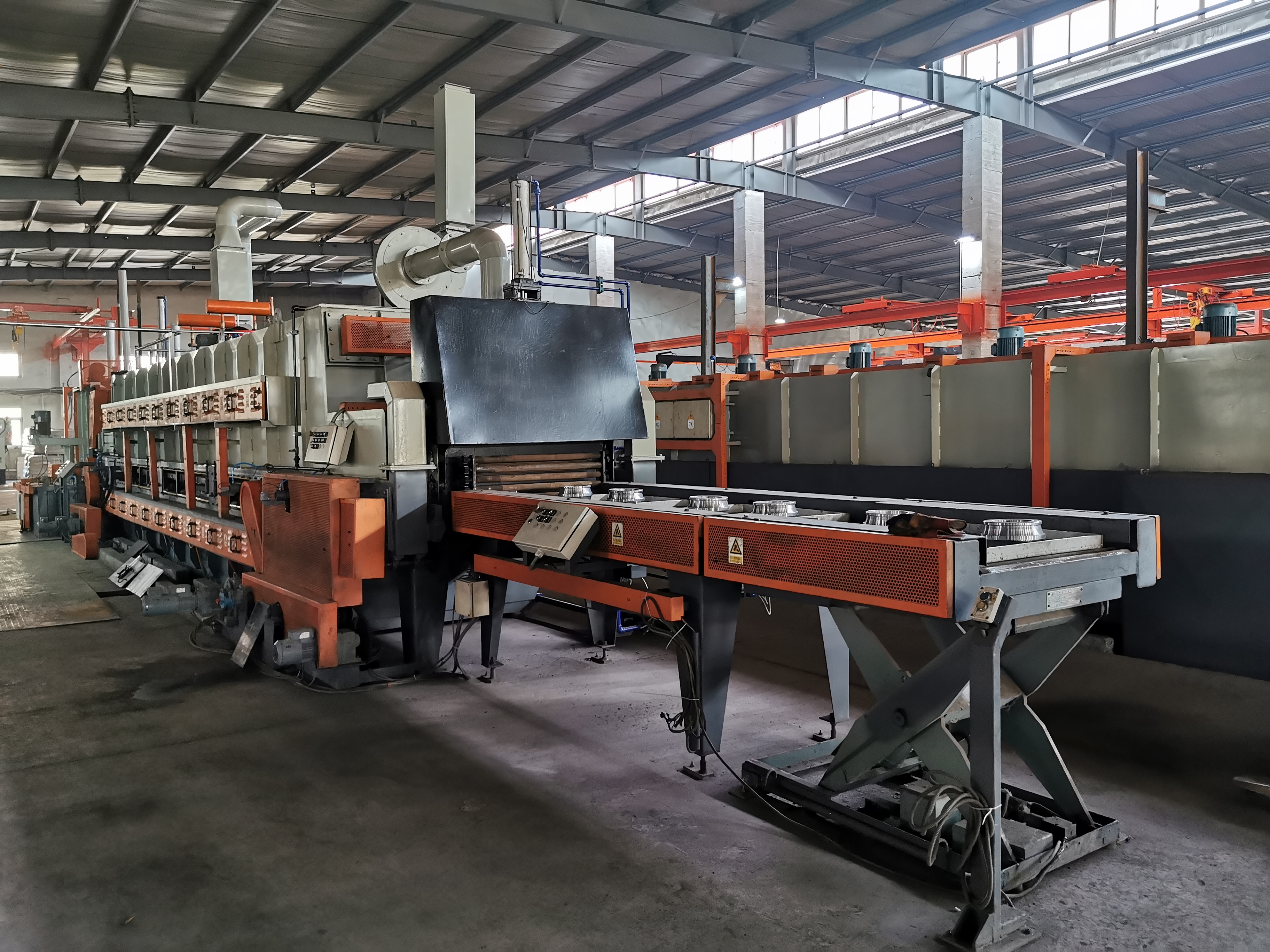
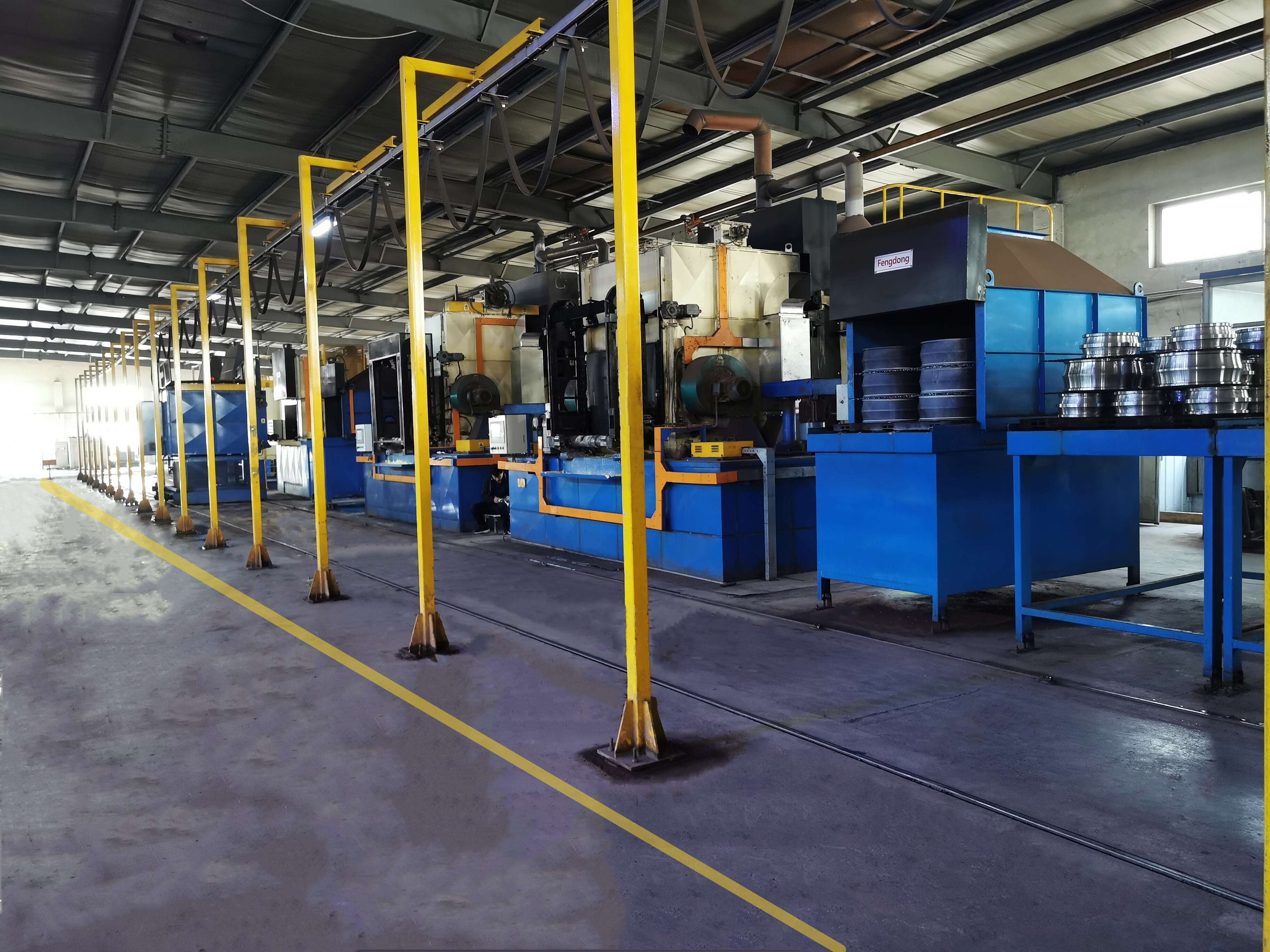
CNC vertical lathe
The machine tool has strong rigidity, high machining accuracy, and stable quality.
Roller quenching
Protective atmosphere quenching, international first-class brand with the same model.
Three heat treatment production lines
Salt bath bainite, martensite
Advanced domestic production lines
Ensure qualified metallographic structure and hardness
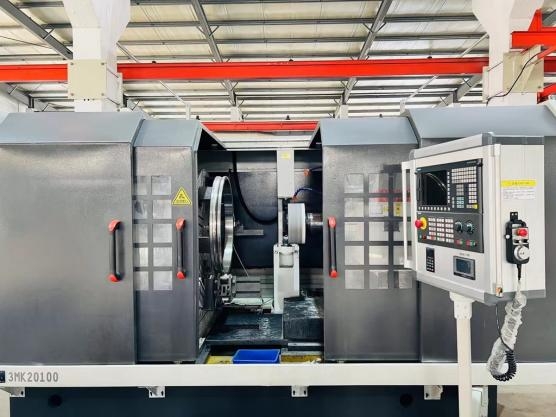
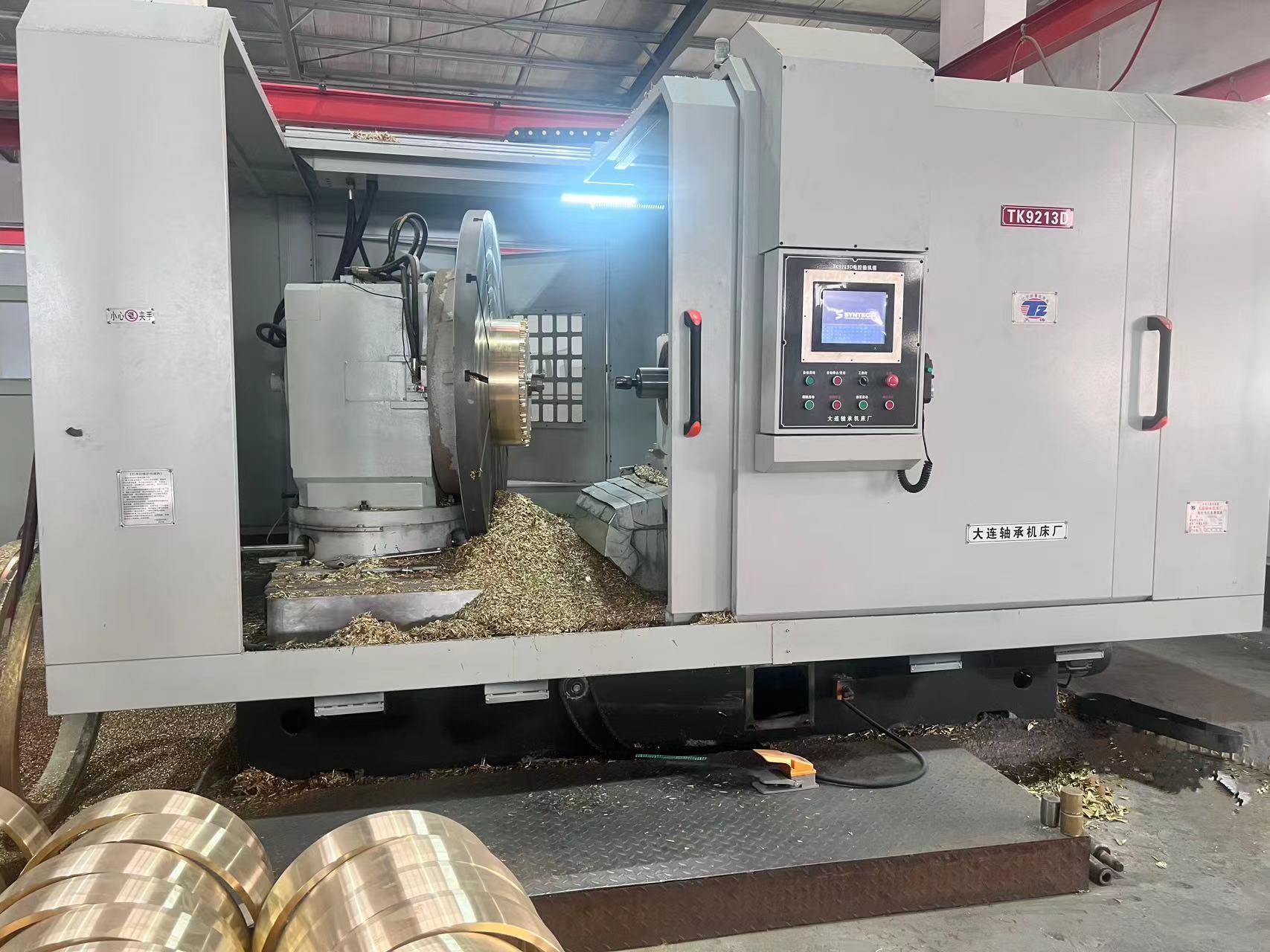
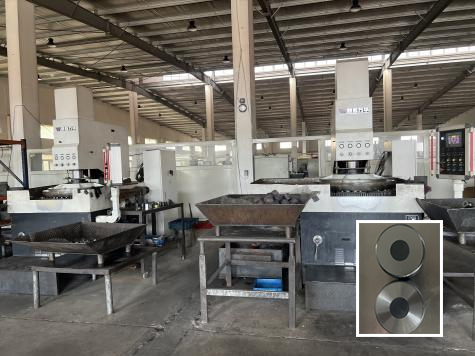
Fine grinding CNC machining
Adopting CNC grinding, the product has high precision and stable quality.
Cage centrifugal casting, precision turning, and CNC boring
All adopt electrolytic copper copper plates and zinc ingots to ensure raw material strength and processing accuracy.
Fine grinding of roller end face
End face height difference within 2 microns.
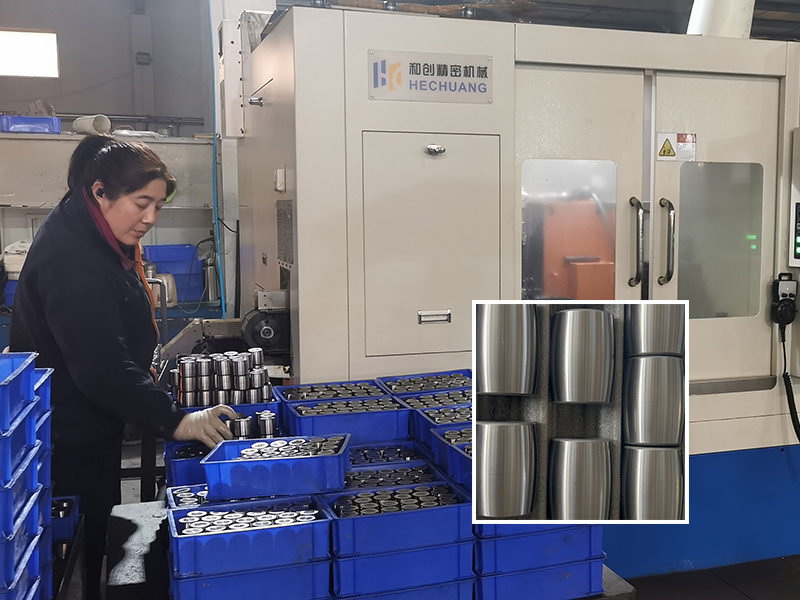
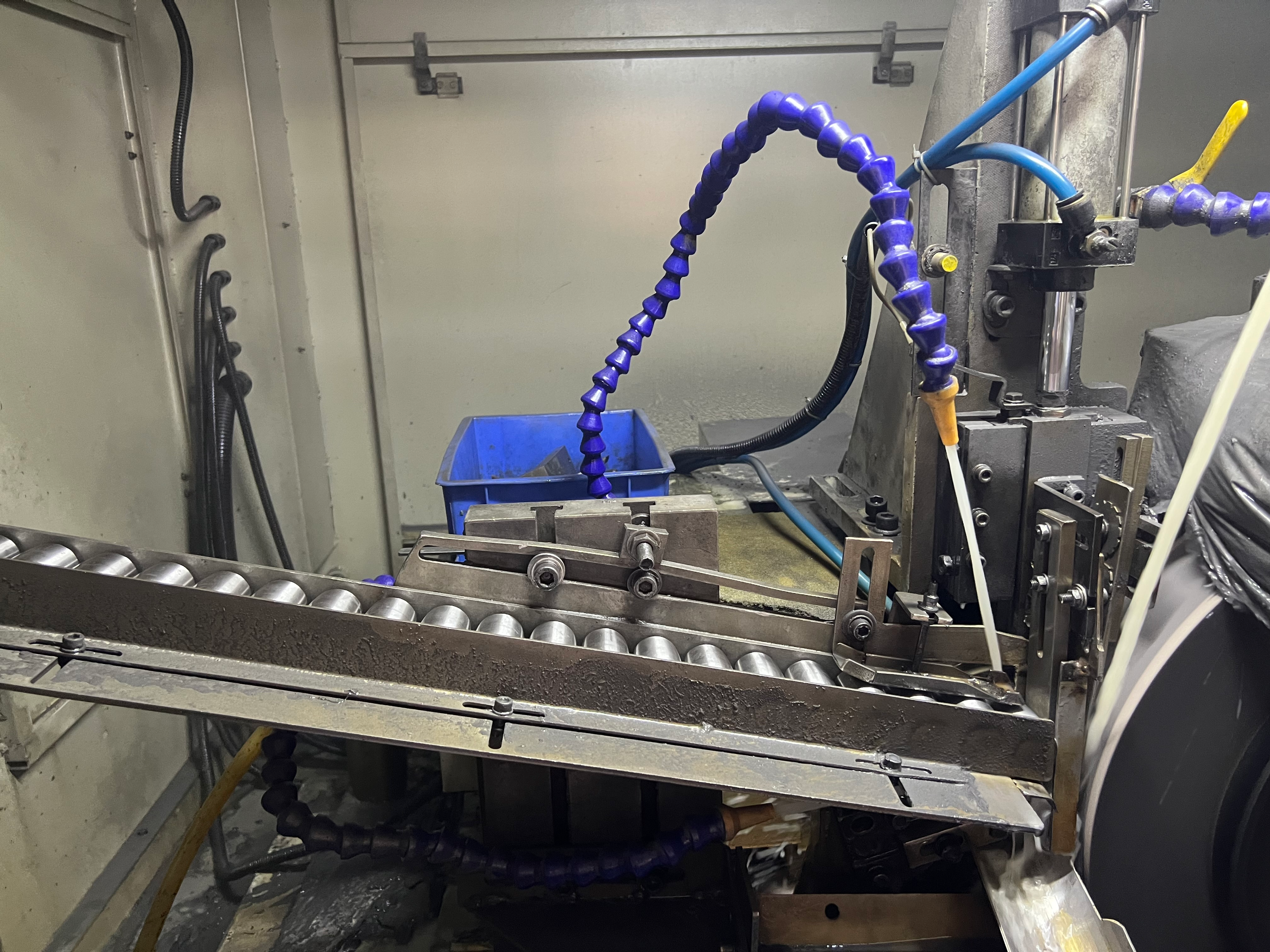
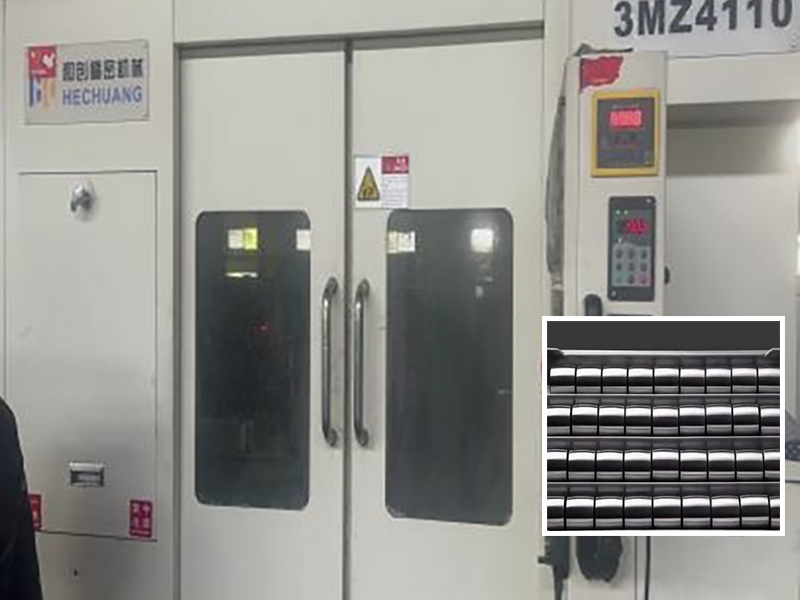
Fine grinding of roller reference surface
High machining accuracy and stable quality.
Fully automatic feeding
Roller precision grinding, all CNC processing, fully automatic online detection.
Roller outer diameter super precision
The outer diameter roughness of the roller is less than 1 micrometer.