Tapered Roller Bearing
Tapered roller bearings are a common type of bearing widely used in various mechanical equipment. It has excellent load carrying capacity and operational stability, suitable for high-speed and high load working environments.
Our tapered roller bearings, designed specifically to handle radial and axial loads, are widely suitable for various applications. Our product specifications vary to ensure they meet the needs of various industries. We only use the highest quality materials and manufacturing processes to ensure the reliability and durability of bearings.
Types of Tapered Roller Bearing
Characteristic: 1. Strong load-bearing capacity: withstand greater radial and axial loads.
2. Easy installation
3. High speed operation
Application: suitable for various large mechanical equipment, such as tower cranes, bridge cranes, steel and metallurgical machinery; heavy-duty mechanical equipment such as excavators, cranes, factory transport vehicles, drilling machines,mining.
Four row tapered roller bearing
Characteristic: 1、Good rolling performance, able to reduce friction loss and energy consumption.
2、Stable movement and low noise can be maintained even at high speeds.
3、Good fault tolerance, able to maintain normal operation when there is a certain deviation in the axial and radial directions
Application:machine tools, metallurgy, mining, petroleum, chemical industry, heavy machinery,large CNC machine tool spindles, heavy conveyors, steel, mining equipment. They are also widely used in high-end fields such as aviation, aerospace, rail transit, etc.
Double row tapered roller bearing
Characteristic: 1、Strong adaptability: have a simple structure, are easy to install and maintain, and are suitable for various industrial applications.
2、Adjusting axial clearance: The internal structure of single row tapered roller bearings can easily adjust the axial clearance to adapt to different working conditions.
Application: widely used in industries such as mechanical manufacturing, power, transportation, metallurgy, mining, etc., to support different types of equipment and machines, such as automobiles, machine tools, ships, motors, etc.
Single row tapered roller bearing
One-stop Solution
We are committed to providing one-stop solutions to meet customer needs. We have a professional technical team that is always available to answer your questions and guide you in choosing the best solution. We focus on customer service and high-quality products to ensure that customers receive the best support and satisfactory service experience.
Our tapered roller bearings are suitable for various industries and provide durable and reliable solutions. We not only provide a wide range of product choices, but also provide customized solutions according to customer needs. Whether you are looking for standard products or customized solutions, we can provide excellent customer service.
Contact us now to learn more about our products and how we can help you find the perfect bearing for your application. We look forward to providing you with high-quality products and satisfactory services.
Application
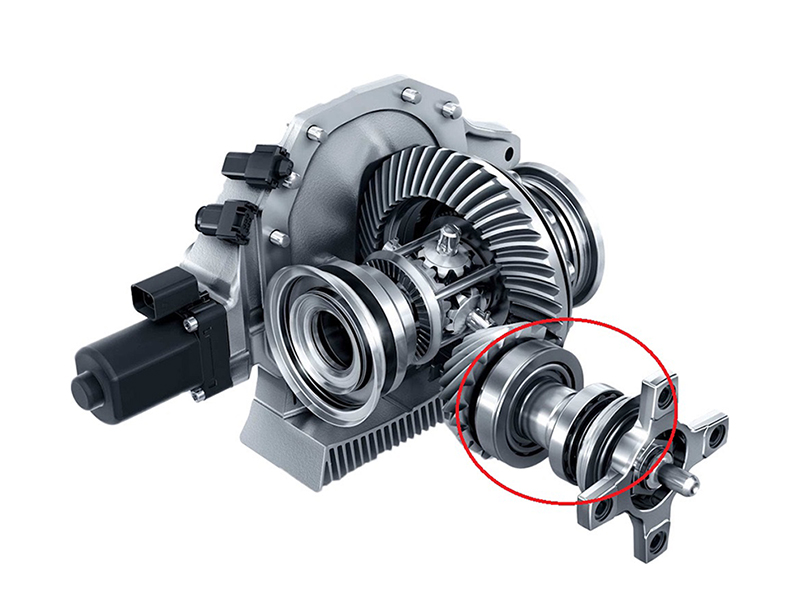
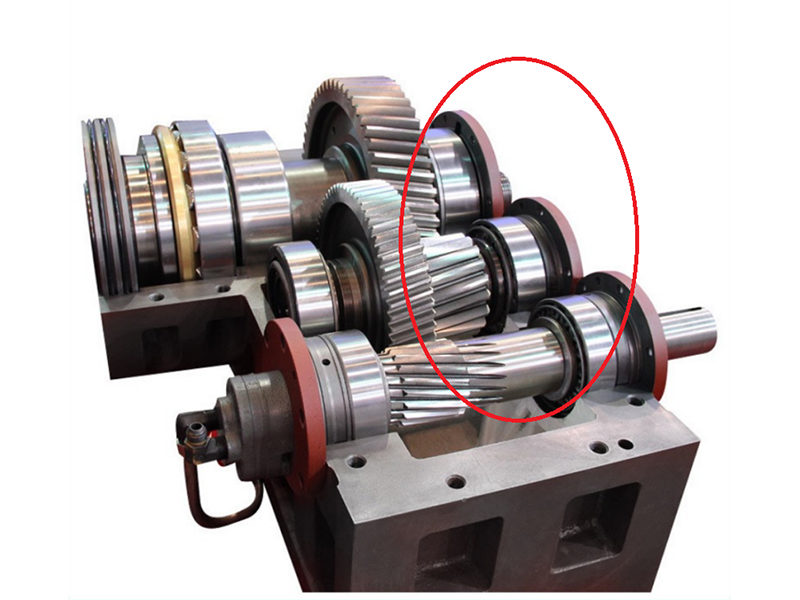
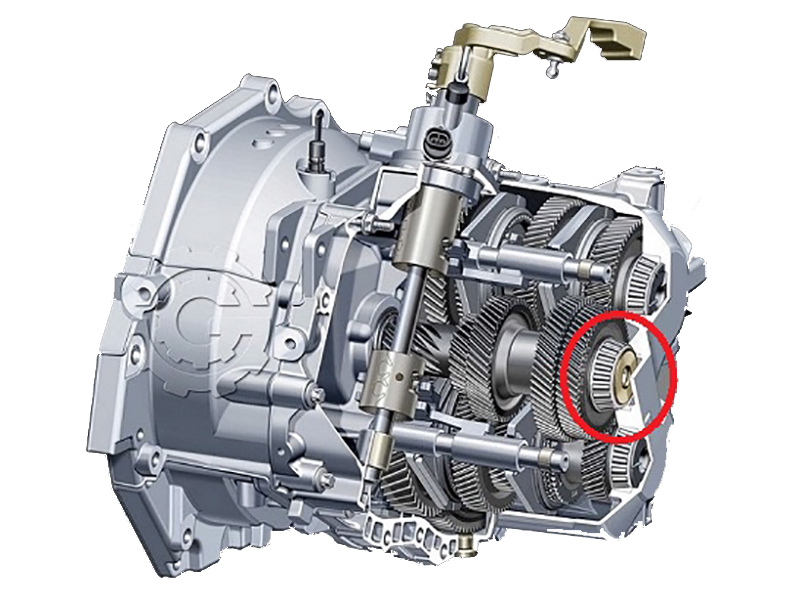
Gearbox
Industrial Gearbox
Automobile Gearbox
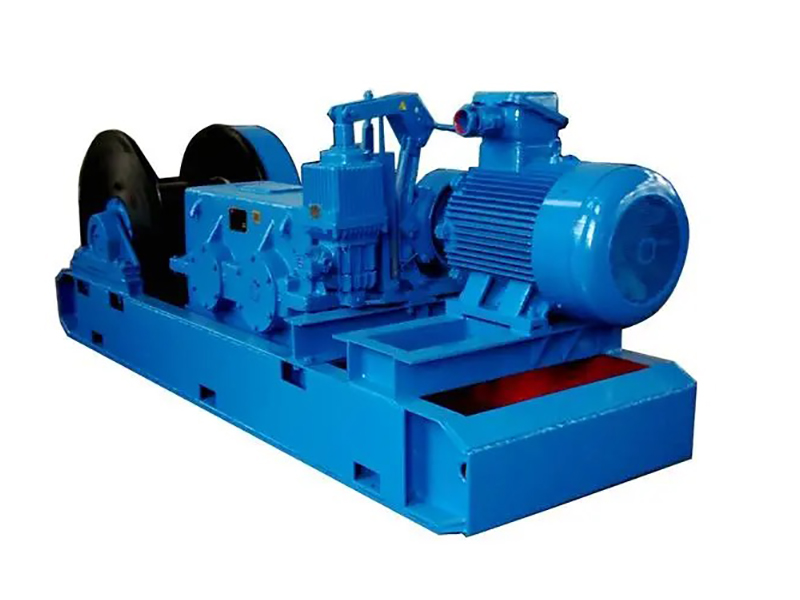
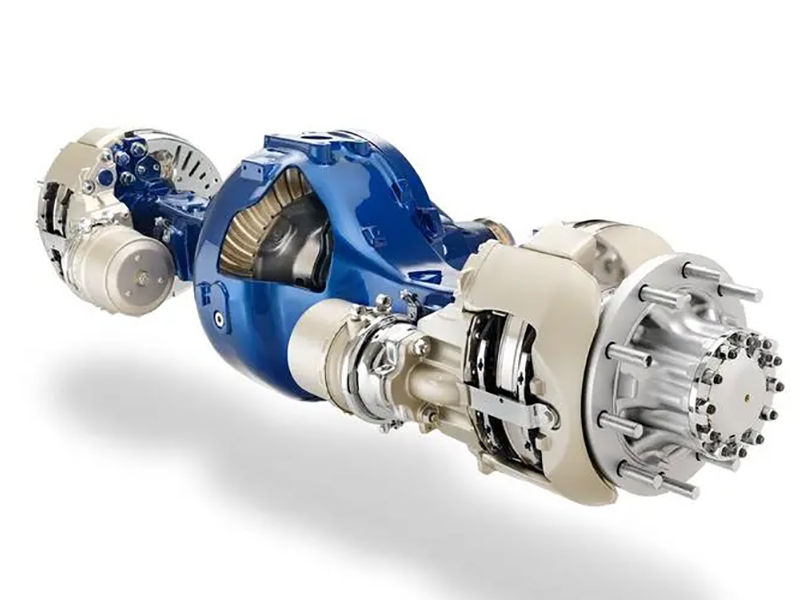
Winch
Axle
CASE SHOW
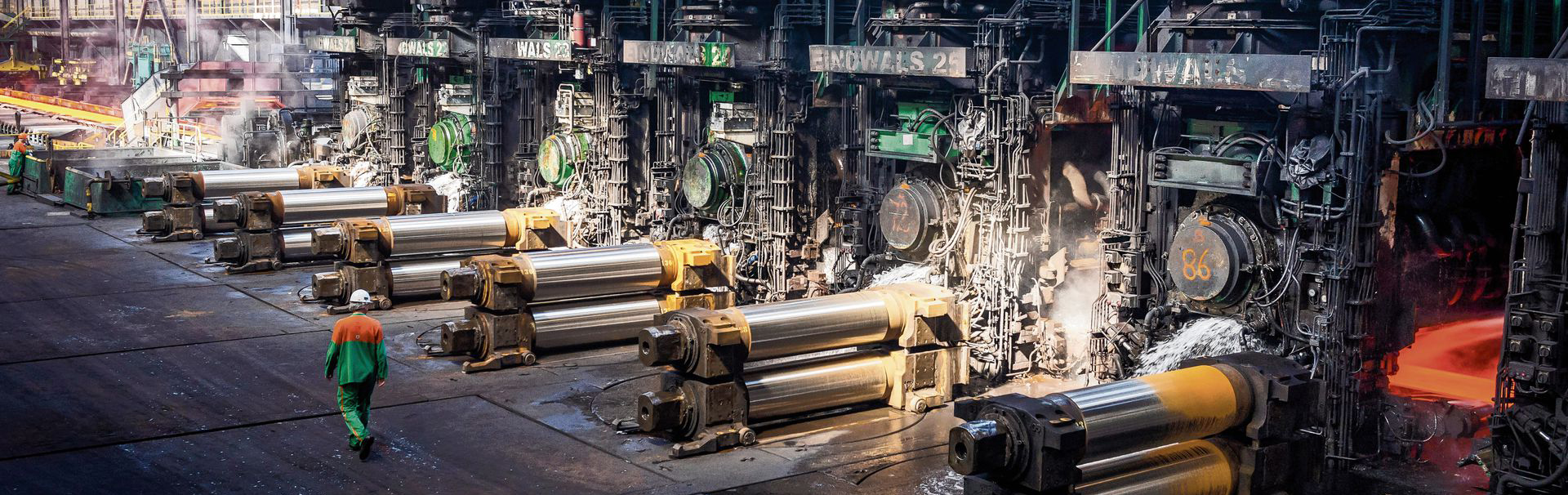
Bearing description: LM761649DW/LM761610-LM761610D four row tapered roller bearing. It has the advantages of low friction coefficient, high transmission efficiency, convenient use and maintenance, and can withstand both radial and axial loads. Due to some improper manufacturing, use, and maintenance processes, bearing failure often occurs.
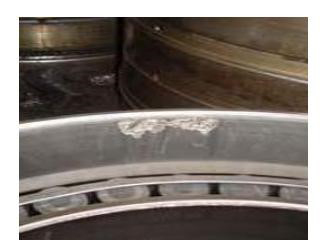
Problem occurred: When the bearing rotates under load, the raceway surface or rolling surface of the inner and outer rings exhibit a fish like peeling phenomenon due to rolling fatigue. The peeling of work roller bearings is generally caused by the following factors: excessive load; Poor installation (non linearity), foreign object intrusion, water ingress; Poor lubrication, lubricant discomfort, and improper bearing clearance; Development caused by rust, erosion points, scratches, and indentations.
Solution: 1. Improving the quality of bearing assembly depends on whether the cleaning method is correct or not. The first step is to determine the cleaning cycle. The original cleaning cycle was 12 months per time on the transmission side of the rolling mill and 6 months per time on the operation side of the rolling mill. The original bearing cleaning cycle did not take into account the maintenance and shutdown of the rolling mill, as well as the maintenance time of the bearings, which cannot truly reflect the usage of the bearings. Based on the actual operating time of the bearings, a new bearing cleaning cycle was developed, and a dedicated person was assigned to track and count the actual operating time of the bearings.
The rolling state is crucial for the use of bearings. One is the issue of installation accuracy, which requires ensuring that the rollers and bearings are axially parallel after installation to avoid cross rolling. The second issue is lubrication. The current oil air lubrication method is oil air lubrication, which has the advantage of generating positive pressure in the bearing box, preventing the emulsion from entering the box, preventing the emulsification of lubricating oil, maintaining a certain oil film, and also cooling the bearing. The domestically produced oil and gas lubrication joint, which was originally used for a long time, has low machining accuracy, poor interchangeability, and is often damaged or blocked, causing poor oil supply to the bearings and oil and gas lubrication alarms. Last year, it was replaced with an imported joint (REBS). After replacement, the number of oil and gas lubrication alarms for the rolling mill was significantly reduced, improving the lubrication effect of the rolling mill work roll bearings. The third issue is the high inclination value during rolling. Conduct a detailed roll shape inspection on each support roller before and after the machine is installed, and record and archive it; In addition to routine inspections before each roll change, a dedicated person will conduct regular spot checks on the bearing seat, upper and lower pads, and rocker plates. Once again, there is the issue of tension fluctuations between frames. By optimizing the tension between rolling mill frames, restoring bilateral tension detection, and regularly calibrating the tension meter, tension roller, and dam roller to ensure consistent tension detection standards. Record and analyze the rolling parameters (inclination value, rolling force deviation, tension, rolling speed, etc.) that reflect the rolling status of the rolling mill.
Improve Effect
Effectively reversed the frequent failure of rolling mill work roll bearings in the past, reducing the consumption of rolling mill work roll bearings by 30.2%
A rough line analysis is conducted on the failure causes and control measures of the work roll bearings in rolling mills. Possible factors that may cause bearing failure are explained, and simple opinions and suggestions are proposed for control measures and methods, which play a role in the correct use of bearings.